The Role of Construction Safety Hubs
In today’s high-risk work environments, especially in construction, effective safety communication is critical to preventing accidents and ensuring regulatory compliance. With the increasing complexity of safety standards, many site managers and heads of safety have turned to centralized platforms, often referred to as “safety hubs,” to streamline the management of critical safety information.
A construction safety hub acts as a central point for displaying fire safety protocols, hazard updates, emergency contacts, and other essential information. Unlike traditional safety noticeboards, these platforms are designed to deliver real-time updates, integrate safety tools, and improve accessibility for workers and inspectors. By enhancing site-wide communication, these hubs help mitigate risks and ensure compliance with regulations from bodies such as the Health and Safety Executive (HSE) and the U.S. Occupational Safety and Health Administration (OSHA).
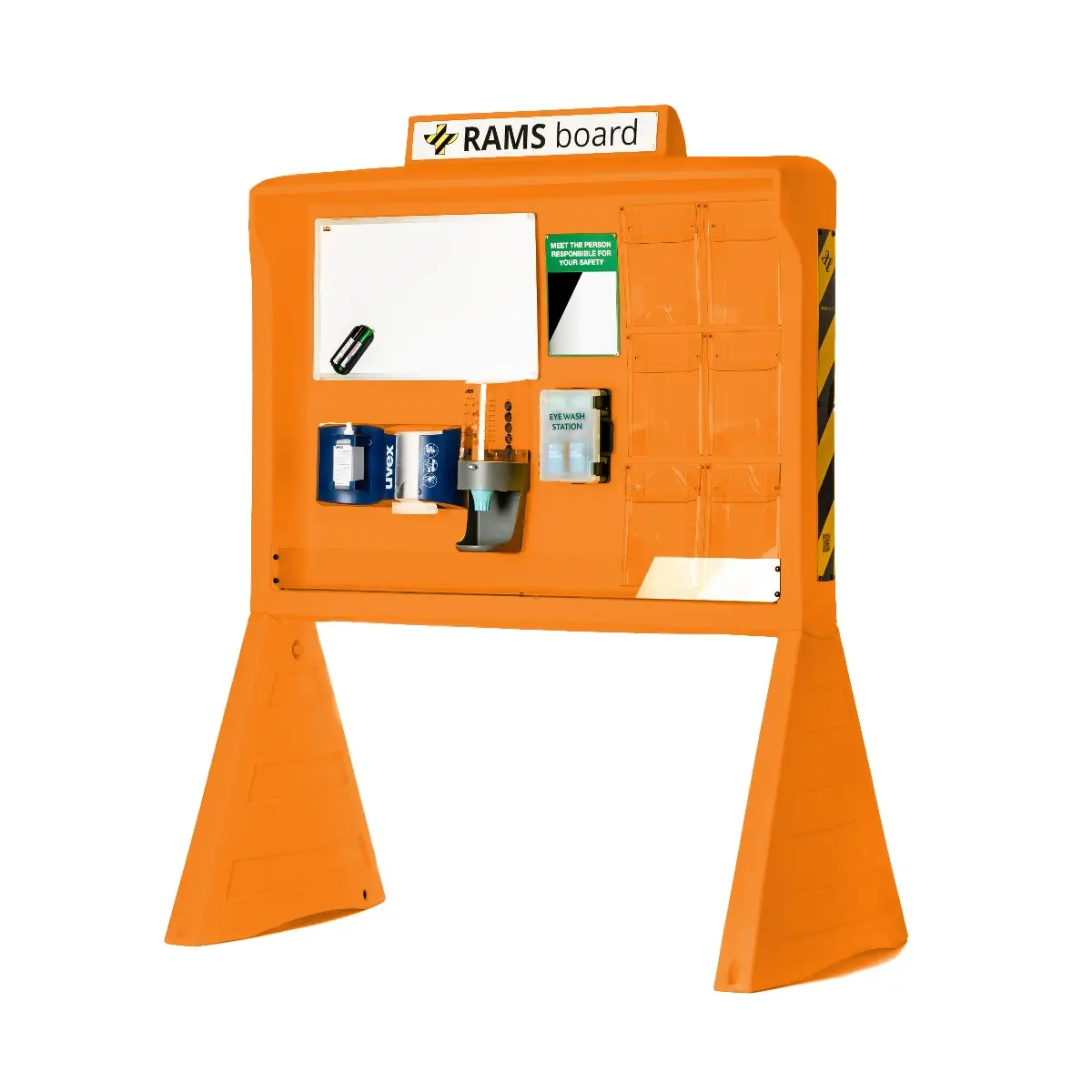
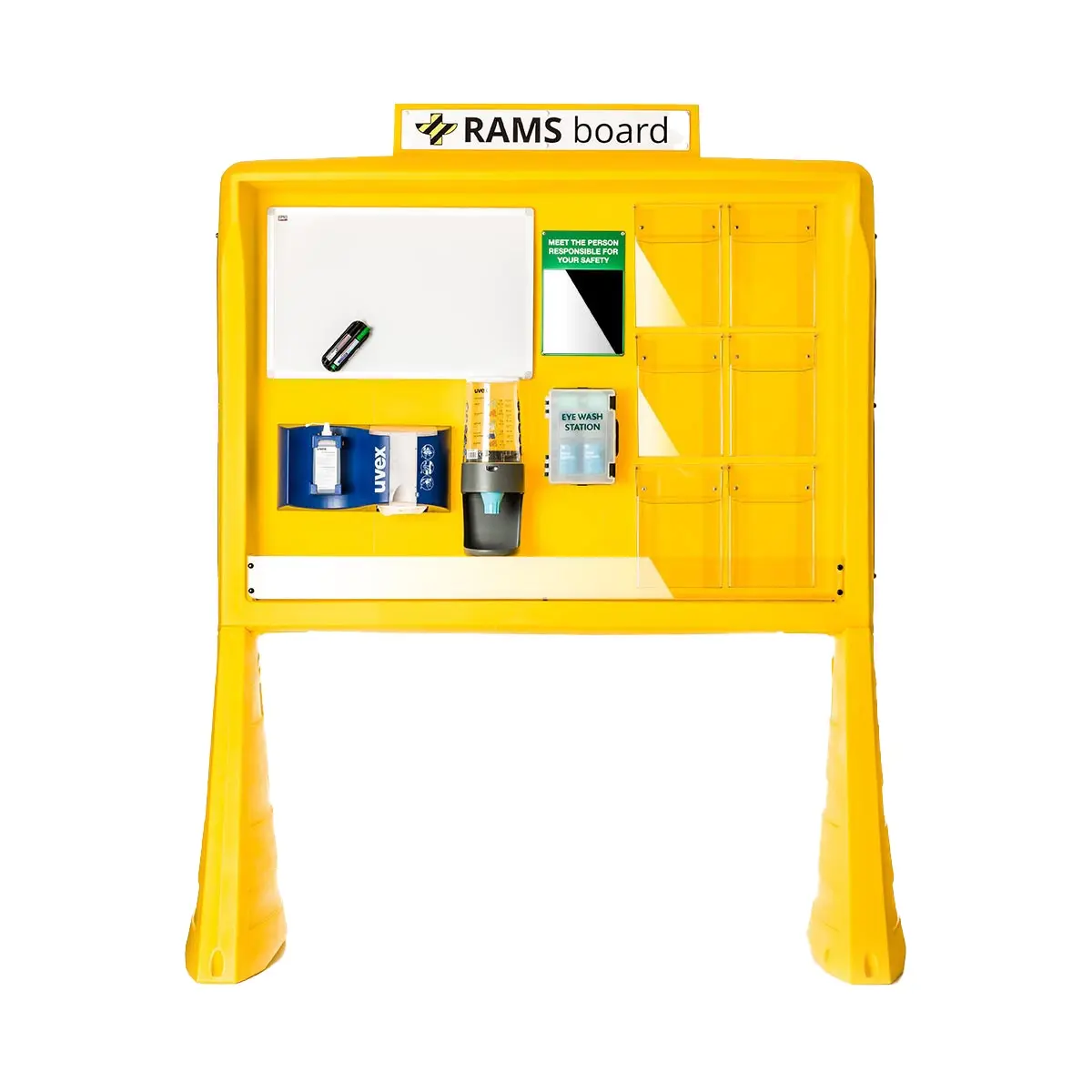
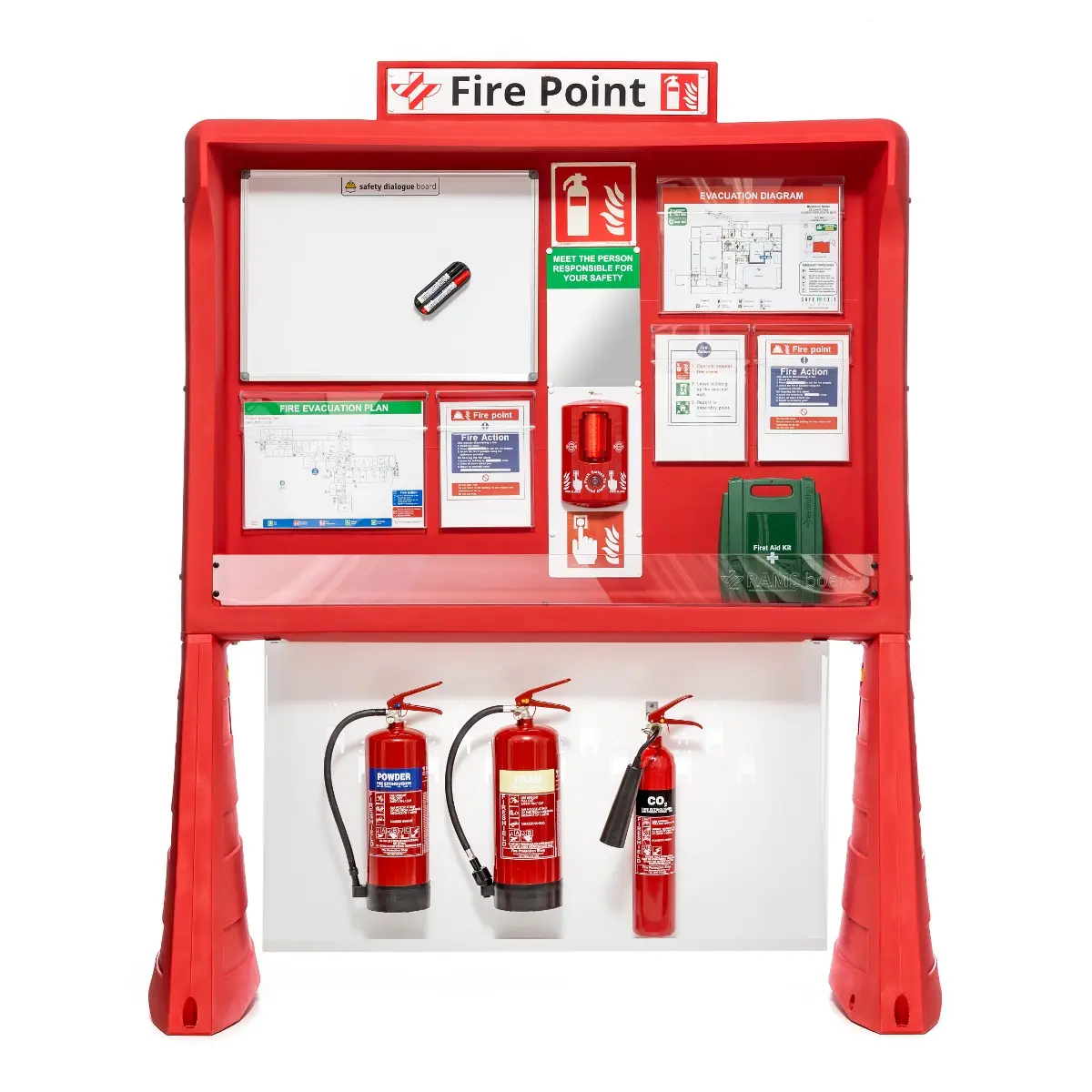
The introduction of advanced safety hubs, such as those offered by platforms like Howler SafetyHub and RAMS Boards, has transformed site safety management. These solutions are tailored to meet the needs of dynamic work environments, offering features such as customizable fire safety points, spill kits, and digital updates. For safety professionals, adopting these platforms is essential to maintaining high safety standards and reducing workplace incidents.
Building Safety Hub and Other Platforms
Several platforms have emerged as leaders in providing comprehensive safety management solutions for the construction and industrial sectors. These platforms cater to the evolving needs of safety officers by offering modular, customizable features that simplify compliance and communication efforts.
- Building Safety Hub: A platform focused on providing guidance and updates for building safety, particularly in residential and commercial developments. It emphasizes fire safety protocols, building code compliance, and risk management strategies tailored to large-scale projects.
- Howler SafetyHub: This product line specializes in fire safety and emergency alarm points for high-risk environments. Howler’s solutions are designed to provide immediate access to fire alarms, extinguishers, and evacuation tools, making them ideal for construction sites that require fast response systems.
- RAMS Boards: Known for their modular, eco-friendly safety boards, RAMS Boards provide a comprehensive solution for construction sites.
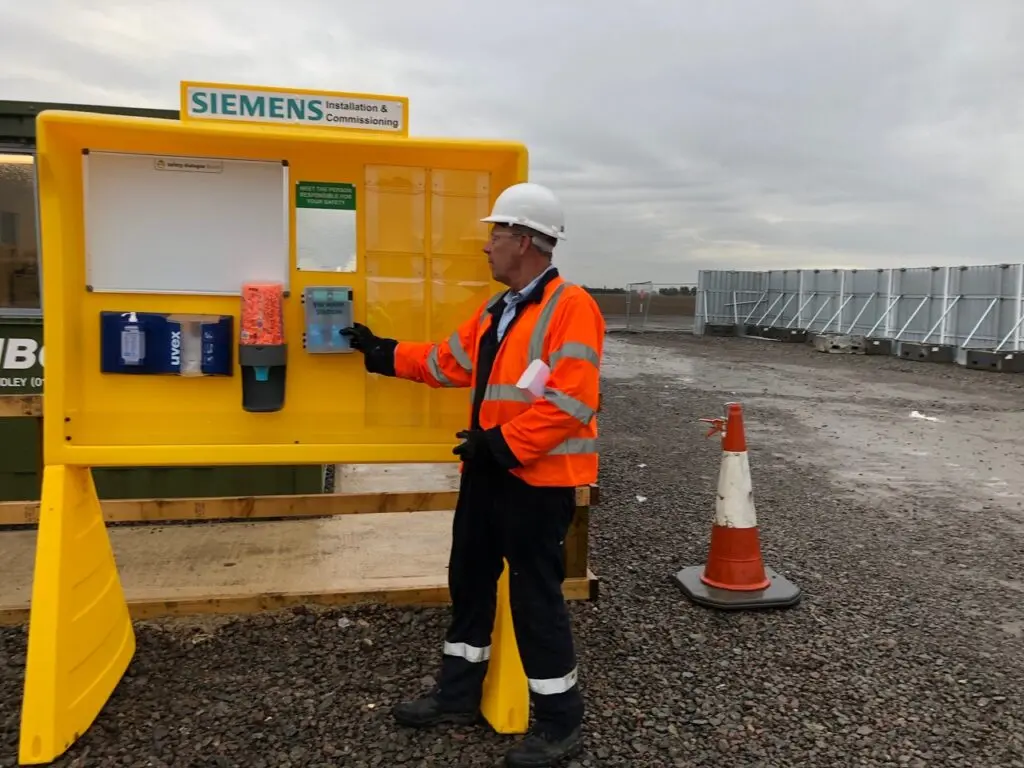
These boards feature integrated components such as fire safety points, spill kits, and transparent pockets for displaying critical documents. Unlike traditional timber or plywood boards, RAMS Boards are weather-resistant, portable, and reusable across multiple projects.
These platforms address common safety communication challenges by centralizing critical information, reducing paperwork, and improving worker engagement. For H&S officers, adopting a safety hub ensures that their teams remain informed and compliant with the latest regulations, reducing the risk of accidents and legal penalties.
Core Functions of a Construction Safety Hub
Construction safety hubs play a vital role in managing workplace hazards, regulatory compliance, and emergency preparedness. These centralized platforms are designed to enhance communication, increase efficiency, and improve worker safety through real-time access to essential information. By organizing key safety protocols and updates in one location, safety hubs help site managers and H&S officers maintain control over safety operations on complex worksites.
Here are the core functions that define an effective construction safety hub:
1. Centralizing Critical Safety Information
A well-designed safety hub serves as a single point of reference for all essential safety documents and notices. On large worksites where risks can change rapidly, having quick access to critical information is crucial. Common elements displayed on a safety hub include:
- Fire Safety Protocols: Evacuation procedures, fire extinguisher locations, and emergency contact numbers.
- Building Codes and Permits: Compliance documentation required for ongoing inspections.
- Hazard Communication: Daily updates on site-specific risks, such as heavy machinery operations, hazardous materials, or restricted zones.
Centralizing this information not only streamlines communication but also ensures that workers and inspectors can easily verify compliance during site visits.
2. Providing Access to Regulatory Updates and Inspection Schedules
Regulations governing construction safety are frequently updated to address new risks, emerging technologies, and industry best practices. Safety hubs help site managers stay informed by providing:
- Real-Time Regulatory Updates: Platforms like Howler SafetyHub are designed to alert users to changes in fire safety and emergency protocols.
- Inspection Schedules and Reports: Modern hubs organize upcoming inspection dates and store records of completed safety audits.
- Automated Compliance Reminders: Notifications for permit renewals, equipment inspections, and safety training sessions reduce the risk of compliance failures.
By integrating these features, safety hubs support continuous improvement in site safety management.
3. Enhancing Worker Safety Communication
Effective safety communication requires more than static documents. Safety hubs offer tools that engage workers and encourage them to stay informed about current risks. Features designed to improve communication include:
- Magnetic or Digital Boards: Allow for frequent updates, such as new hazard alerts or changes to site layouts.
- Visual Cues and Symbols: Clear, color-coded sections for fire safety, emergency contacts, and equipment guidelines help workers quickly find relevant information.
- Customized Notifications: Safety hubs can be tailored to highlight specific safety needs for a project, such as confined space entry protocols or crane operation risks.
By fostering better communication, these platforms help reduce confusion and improve compliance with safety procedures.
4. Integrating Emergency Preparedness Tools
Emergency response is a critical function of any construction safety platform. In high-risk industries, the ability to respond quickly to incidents can prevent injuries and save lives. Safety hubs typically integrate essential emergency preparedness tools, including:
- Fire Alarm Points: Systems like those offered by Howler SafetyHub allow workers to raise alarms at designated safety stations.
- Spill Kits and Fire Extinguishers: Platforms such as RAMS Boards offer modular features that include options for emergency equipment like spill containment kits and fire extinguishers.
- Evacuation Diagrams: Visual evacuation routes help workers and visitors quickly locate safe exits during emergencies.
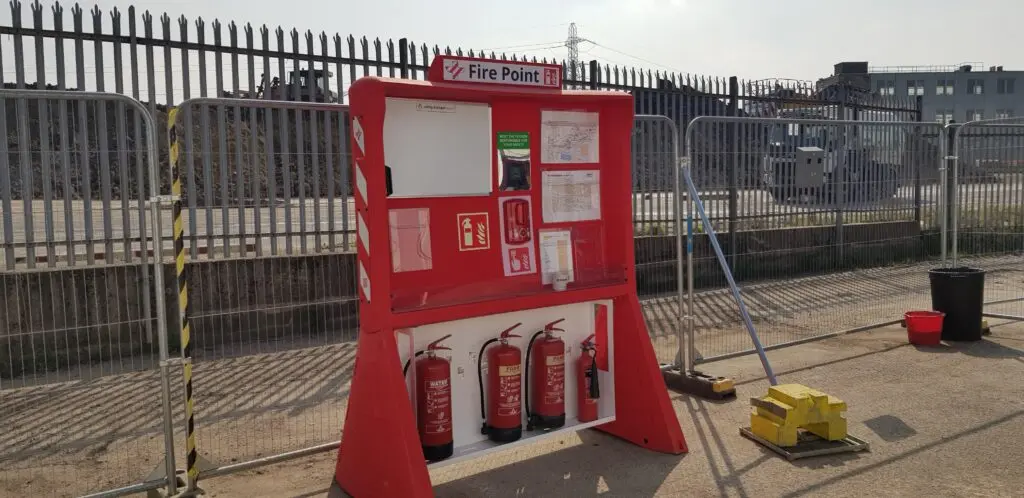
These features ensure that both workers and site managers are prepared to handle incidents efficiently and in compliance with safety regulations.
5. Document Organization and Protection
Keeping safety documents organized and protected from environmental damage is a common challenge on construction sites. Traditional noticeboards often become cluttered, worn, or difficult to read, compromising their effectiveness. Modern safety hubs, on the other hand, include:
- Transparent Document Pockets: Weatherproof covers that shield risk assessments, permits, and emergency procedures from dust and moisture.
- Dedicated Sections: Separate areas for different document types, ensuring that key information is easy to locate and access.
- Digital Document Storage: Some platforms offer QR codes that link to online databases where workers can access detailed documents from their mobile devices.
This organization reduces the time spent searching for important information and improves the site’s overall safety performance.
Managing Fire Safety and Emergency Preparedness
Fire safety and emergency preparedness are critical components of any construction safety strategy. Construction sites are particularly vulnerable to fire risks due to the presence of flammable materials, electrical hazards, and heavy machinery. A well-implemented safety hub centralizes fire safety information and tools, making it easier for workers to respond quickly and effectively in emergency situations. By integrating real-time communication, fire safety protocols, and emergency equipment, modern platforms help site managers maintain compliance and reduce risk.
1. Fire Safety Protocols and Regulatory Compliance
Construction safety hubs ensure that fire safety procedures are clearly communicated to all site personnel. This includes:
- Evacuation Procedures: Clearly marked routes and assembly points displayed on site maps, ensuring that workers know the safest exit paths in case of fire.
- Fire Watch Requirements: On high-risk projects, fire watches may be mandatory to monitor potential ignition points. Platforms like Howler SafetyHub provide monitoring stations equipped with fire alarms and other alert systems.
- Regulatory Compliance Documentation: Fire safety hubs store permits, inspection reports, and certificates needed to pass regulatory audits, reducing the risk of compliance violations.
Maintaining well-documented and accessible fire safety information helps companies meet the requirements of authorities like the Health and Safety Executive (HSE) and the National Fire Protection Association (NFPA).
2. Integration of Emergency Equipment
Having immediate access to emergency equipment is vital during fire-related incidents. Safety hubs offer modular solutions to integrate key safety resources, such as:
- Fire Extinguisher Stands: Platforms like RAMS Boards provide options to attach fire extinguishers directly to the hub, ensuring they are easily accessible during an emergency.
- Alarm Systems: Howler’s safety hubs are designed with push-button fire alarms that alert workers across large worksites. These systems can also trigger evacuation alerts.
- Spill Kits: In projects involving hazardous materials, spill kits are crucial for managing both chemical and fire-related risks. RAMS Boards offer the flexibility to add spill kits and other emergency tools to their setups.
By consolidating these safety resources in one location, safety hubs enhance emergency preparedness and reduce response times.
3. Real-Time Hazard Updates
Construction sites are dynamic, with new fire risks emerging as projects progress. Real-time communication is essential to ensure that workers remain aware of these risks. Modern safety hubs support real-time updates through features such as:
- Magnetic Whiteboards: Allow site managers to post daily updates on fire risks, such as ongoing hot work operations (welding, cutting, etc.).
- Digital Alerts: Advanced hubs can send notifications to workers’ mobile devices, alerting them to fire risks or evacuation drills.
- Inspection and Risk Assessment Updates: Regular updates to fire risk assessments are posted on-site to reflect changing conditions and project milestones.
By ensuring that fire safety information is continuously updated, these platforms help workers make informed decisions that reduce the likelihood of fire incidents.
4. Training and Drills
Effective emergency preparedness depends on regular training and practice. Safety hubs facilitate this by providing access to training materials and schedules for drills. Components that support fire safety training include:
- Evacuation Diagrams: Visual aids showing escape routes and assembly points, ensuring workers understand the procedures.
- Safety Briefing Materials: Platforms allow safety managers to display or distribute information on fire hazards, emergency contacts, and response protocols.
- Fire Drill Scheduling: Automated reminders help site managers plan and conduct regular fire drills, reinforcing worker preparedness.
Consistent training and drills improve response times and worker confidence, reducing the risk of injuries during actual emergencies.
5. Fire Safety as Part of a Broader Emergency Strategy
Fire safety is just one aspect of a comprehensive emergency preparedness plan. Construction safety hubs are designed to manage multiple types of emergencies, including chemical spills, medical incidents, and severe weather events. Features that enhance overall emergency management include:
- All-Hazard Communication: Platforms provide sections dedicated to various types of emergencies, ensuring that workers are prepared for any incident.
- Emergency Contact Lists: Quick access to first responders, site safety officers, and medical personnel helps streamline emergency communication.
- Coordination with Local Authorities: Safety hubs facilitate collaboration with fire departments and regulatory agencies by providing up-to-date compliance records and site plans.
By adopting a holistic approach to emergency management, companies can reduce risks and demonstrate a strong commitment to worker safety. Construction safety hubs that emphasize fire safety and emergency preparedness play a critical role in reducing risks and ensuring compliance. These platforms equip workers with the tools and information needed to respond quickly and effectively to emergencies, ultimately improving site safety performance.
Ensuring Compliance Through Centralized Platforms
Maintaining regulatory compliance is a core responsibility for site managers and heads of safety in the construction industry. Non-compliance can lead to severe consequences, including fines, project delays, and increased accident risks. Centralized safety hubs streamline compliance efforts by organizing key documentation, automating reminders for inspections, and facilitating audits. By centralizing critical safety information, companies can stay ahead of regulatory requirements while promoting a culture of safety.
1. Organizing Essential Compliance Documents
One of the biggest challenges on construction sites is ensuring that mandatory safety documents are consistently available and up-to-date. Safety hubs address this challenge by offering a structured system for document organization and protection. Commonly displayed compliance documents include:
- Risk Assessments and Method Statements (RAMS): Required to identify site-specific hazards and the measures taken to control them.
- Permits to Work: Documentation needed for high-risk activities, such as hot works, confined space entry, and crane operations.
- Inspection Records: Logs of safety inspections, including fire safety checks, equipment maintenance, and health audits.
- Employer’s Liability Insurance Certificates: Legally mandated to demonstrate that workers are insured in case of injury or illness.
Modern safety hubs, like RAMS Boards, feature transparent, weather-resistant document holders that protect these records from damage. By ensuring that documents are accessible and legible, safety hubs make it easier to comply with site inspections and audits.
2. Automating Compliance Tasks
Manual tracking of permits, inspections, and certifications can be time-consuming and prone to errors. Advanced safety hubs help automate these tasks by integrating reminders and alerts for key compliance milestones. Features that enhance automation include:
- Inspection and Permit Reminders: Notifications alert site managers when permits need renewal or when the next scheduled inspection is approaching.
- Centralized Inspection Reports: Platforms like the Howler SafetyHub store completed safety reports, making them easily retrievable during audits.
- Real-Time Monitoring: Some digital safety hubs can track site conditions and equipment performance, providing instant updates if compliance thresholds are breached (e.g., noise levels or air quality).
These automation features reduce administrative workload and ensure that compliance requirements are consistently met.
3. Facilitating Site Inspections and Audits
Regulatory authorities frequently conduct unannounced inspections to ensure that construction sites adhere to safety standards. Inspectors evaluate factors such as document availability, fire safety preparedness, and adherence to risk management protocols. Well-organized safety hubs can significantly simplify the inspection process by:
- Providing Instant Access to Compliance Records: Documents such as risk assessments, permits, and inspection logs are centralized, allowing inspectors to verify compliance without delays.
- Highlighting Fire Safety Measures: Integrated fire safety points with extinguishers, alarms, and evacuation routes are immediately visible, reinforcing the site’s readiness for emergencies.
- Demonstrating a Proactive Approach: Regular updates to safety hubs indicate that site managers are actively monitoring risks and adhering to best practices.
Many companies that adopt platforms like RAMS Boards report smoother inspections and reduced regulatory penalties, as inspectors view well-maintained hubs as evidence of effective safety management.
4. Displaying Mandatory Safety Notices
Certain safety notices are legally required to be displayed on construction sites, including:
- The Health and Safety Law Poster: Outlining workers’ rights and responsibilities under safety regulations.
- First Aid and Emergency Contact Information: Listing site-specific first responders and nearby medical services.
- Evacuation Procedures: Visual guides that detail escape routes and assembly points for fire and other emergencies.
Safety hubs ensure that these notices remain prominently displayed and easily accessible, supporting both legal compliance and worker awareness.
5. Improving Safety Accountability
Compliance extends beyond documentation—it also requires worker engagement and accountability. By maintaining visible, well-organized safety hubs, site managers encourage workers to stay informed and follow protocols. Platforms like RAMS Boards and Howler SafetyHub reinforce this engagement through:
- Motivational Messages: For example, RAMS Boards feature mirrors with the message “Meet the person responsible for your safety,” prompting workers to reflect on their actions.
- Dynamic Updates: Real-time hazard alerts and safety announcements keep workers aware of current risks and procedures.
- Safety Performance Metrics: Some digital platforms track and display key metrics, such as days without incidents or inspection scores, reinforcing a sense of responsibility among workers.
This emphasis on accountability helps build a culture of safety where compliance becomes a shared responsibility across the workforce.
6. Reducing Non-Compliance Risks
Failure to comply with safety regulations can result in significant financial and legal repercussions. Centralized safety hubs reduce these risks by minimizing administrative errors, ensuring documents are always updated, and supporting a proactive approach to risk management. Companies that invest in these platforms often experience:
- Fewer Inspection Failures: Well-organized safety records improve audit outcomes and reduce penalties.
- Lower Incident Rates: Effective safety communication helps prevent accidents, reducing both injury risks and liability exposure.
- Improved Reputation: Consistent compliance demonstrates a company’s commitment to worker safety, which can enhance its credibility with clients, regulators, and industry partners.
By integrating compliance tasks into a single, easily managed platform, construction safety hubs empower site managers to maintain high safety standards with greater efficiency.
Customization and Industry Tools
One of the key advantages of modern construction safety hubs is their ability to be customized according to project-specific needs. Customization enables site managers to prioritize the most relevant safety information and tools for their particular environment, which improves worker engagement, hazard management, and regulatory compliance. Additionally, these hubs often integrate industry tools designed to enhance on-site safety, such as fire safety points, spill kits, and emergency response features.
Platforms like RAMS Boards and Howler SafetyHub offer flexible solutions that allow companies to tailor their safety infrastructure, ensuring that communication and preparedness remain effective in diverse work settings.
1. Custom Layouts for Site-Specific Needs
Different worksites present unique risks, and a one-size-fits-all approach to safety communication can be ineffective. Custom safety hubs address this issue by offering a variety of configurations that can adapt to site requirements. Examples of customization include:
- Hazard Prioritization: For sites with specific risks—such as chemical handling or heavy machinery operations—safety hubs can highlight those hazards with color-coded alerts and specialized signage.
- Location-Specific Information: Fire evacuation plans, restricted access zones, and emergency contacts can be tailored to reflect the physical layout and risks of the site.
- Document Segregation: Platforms like RAMS Boards provide separate, transparent pockets for different document categories (e.g., risk assessments, permits, and inspection records), making it easy for workers and inspectors to find relevant information.
By customizing the safety hub layout, site managers can ensure that workers are exposed to the most critical safety information every day.
2. Integration with Emergency Tools
Modern safety hubs are designed to function as centralized emergency stations. Instead of scattering fire safety equipment or spill kits across a site, companies can integrate these tools directly into the hub. This approach improves both accessibility and response times.
Key emergency tools that can be integrated include:
- Fire Safety Points: Howler SafetyHub systems feature fire alarm points that are strategically positioned for quick access on large worksites.
- Spill Kits: RAMS Boards offer optional modules for adding spill containment kits, which are essential on sites dealing with hazardous chemicals.
- First Aid and Eye Wash Stations: Some hubs include built-in stations that provide workers with immediate access to medical supplies in case of injury.
This integration allows for better coordination during emergencies and helps meet regulatory requirements for fire and occupational safety.
3. Customizable Alerts and Notifications
Safety communication is most effective when it can adapt to changing conditions. Custom safety hubs enable site managers to post dynamic updates using features like:
- Magnetic Whiteboards: Easily reconfigurable boards allow for daily updates on risks, project milestones, and equipment movement.
- Digital Alerts: Advanced platforms offer mobile alerts that notify workers of new hazards, such as extreme weather conditions or high-risk operations.
- Hazard Tracking: By linking with workplace management systems, some hubs can generate automatic alerts when certain safety conditions are met, such as exceeding noise or temperature thresholds.
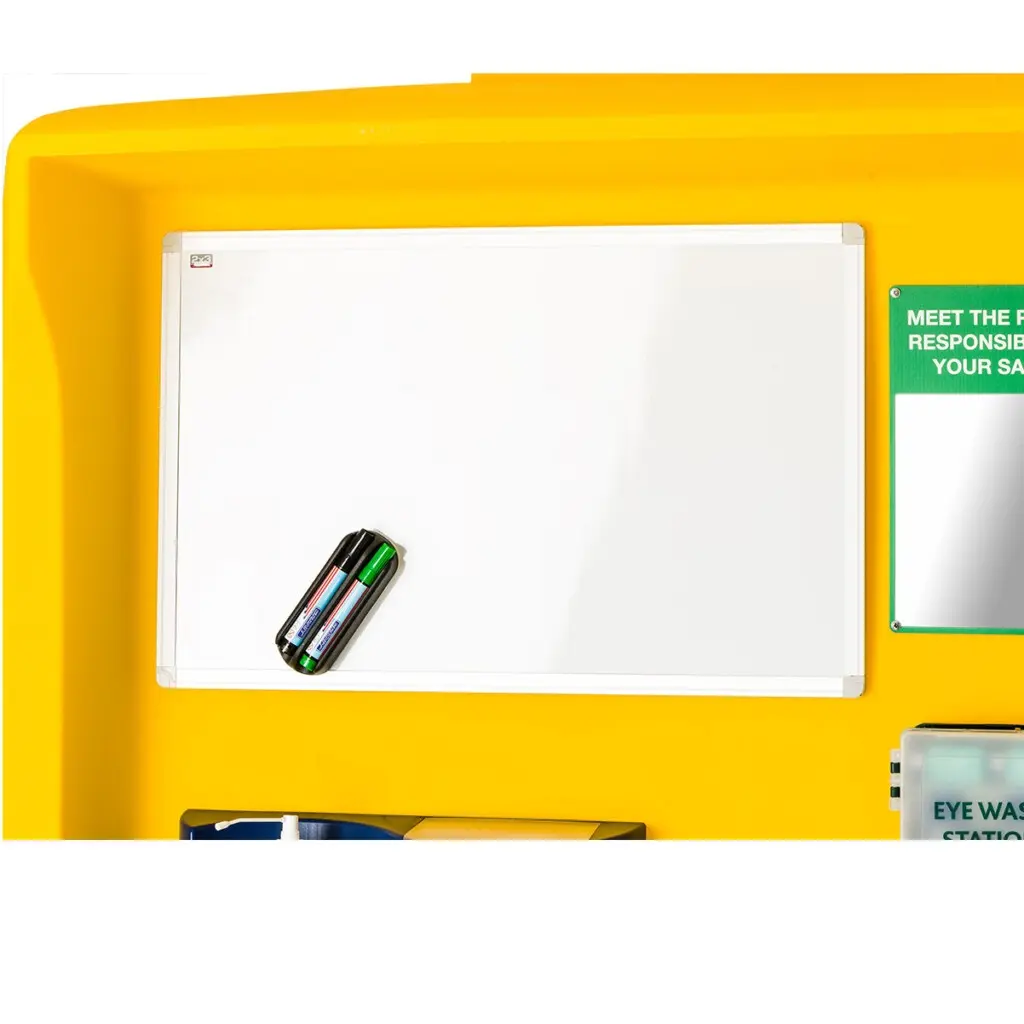
These tools ensure that workers remain informed and prepared for evolving risks, reducing the likelihood of accidents caused by outdated information.
4. Branding and Corporate Identity
For large companies, safety hubs can also serve as a tool to promote corporate identity and values. Customization options may include:
- Logos and Brand Colors: Displaying a company’s branding on the safety hub reinforces the organization’s commitment to safety.
- Safety Messaging: Custom motivational slogans and behavioral prompts, such as “Your safety matters here,” can help foster a positive safety culture.
- Recognition Programs: Hubs can feature sections dedicated to showcasing safety achievements, such as days without incidents or worker recognition awards.
This customization improves engagement by making the safety hub an integral part of the company’s safety initiatives and identity.
5. Industry-Specific Safety Features
Certain industries require highly specialized safety features that go beyond standard protocols. Construction and industrial sites, for example, often need tools to manage high-risk tasks such as confined space entry, crane operations, and demolition work. Custom safety hubs can support these tasks by:
- Displaying Specialized Permits: Custom document holders can be designed to prominently feature permits required for tasks like electrical work or hazardous material handling.
- Equipment Integration: Platforms like Howler SafetyHub are equipped to support multiple fire alarms and detection devices across large or multi-level sites.
- Site Safety Plans: Custom hubs can display large, detailed maps of multi-site operations, showing hazard zones and access points for coordination between teams.
By addressing the specific safety challenges of each industry, customized hubs enhance both compliance and efficiency, minimizing risks for complex projects.
6. Enhancing Worker Accessibility
Custom safety hubs are also designed with worker accessibility in mind. This includes ensuring that information is easy to read and equipment is easy to reach for all personnel. Features that support accessibility include:
- Clear Visual Hierarchies: Sections are organized by priority, with critical safety information (e.g., emergency contacts) placed at eye level.
- Multilingual Support: For sites with a diverse workforce, safety hubs can display key messages and documents in multiple languages to ensure full comprehension.
- Ergonomic Design: Tools such as fire alarms and first aid kits are placed at optimal heights to facilitate quick access, even in stressful situations.
Customization is a crucial aspect of modern construction safety hubs, allowing companies to address unique risks, comply with regulatory standards, and engage workers more effectively.
Real-World Applications of Construction Safety Hubs
Construction safety hubs have proven their effectiveness across various projects by improving compliance, enhancing worker safety, and streamlining communication. Real-world applications show how customized safety platforms, such as RAMS Boards and Howler SafetyHub, can address site-specific challenges and promote a culture of safety. By integrating emergency tools, real-time updates, and regulatory compliance resources, these hubs have become indispensable on large-scale construction and industrial projects.
1. Case Study: Large Infrastructure Project with RAMS Boards
A major infrastructure company working on a rail expansion project faced multiple compliance challenges. Traditional plywood noticeboards deteriorated under harsh weather conditions, making safety documents difficult to access and leading to poor inspection outcomes. Workers often complained about confusion regarding site-specific safety procedures.
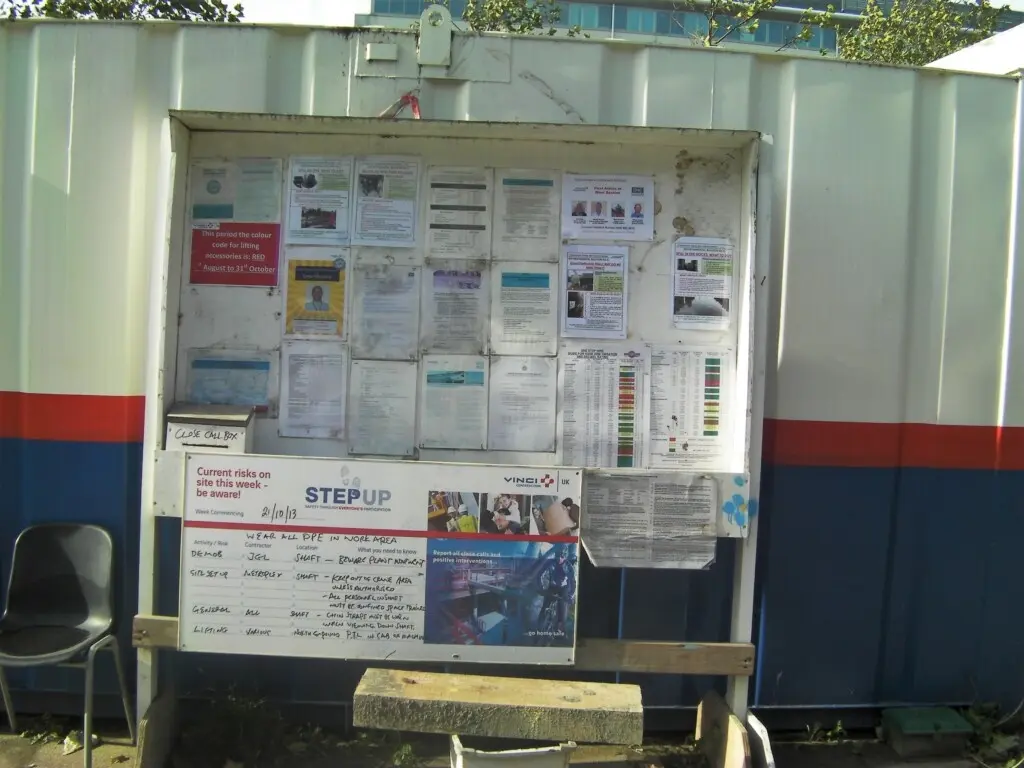
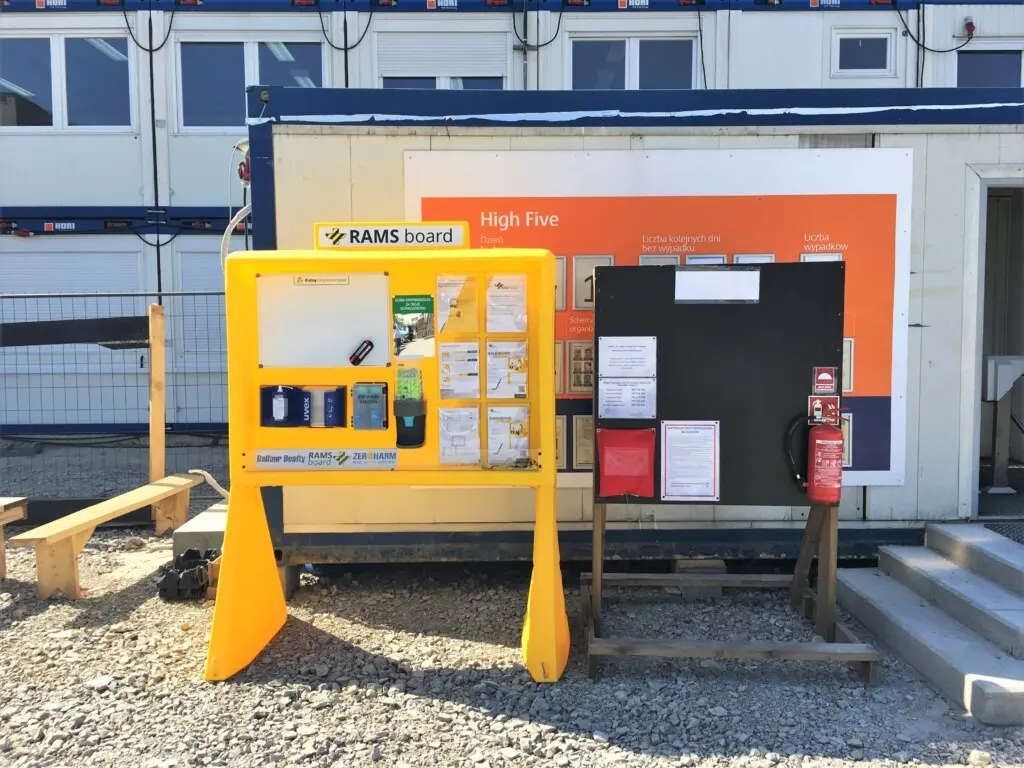
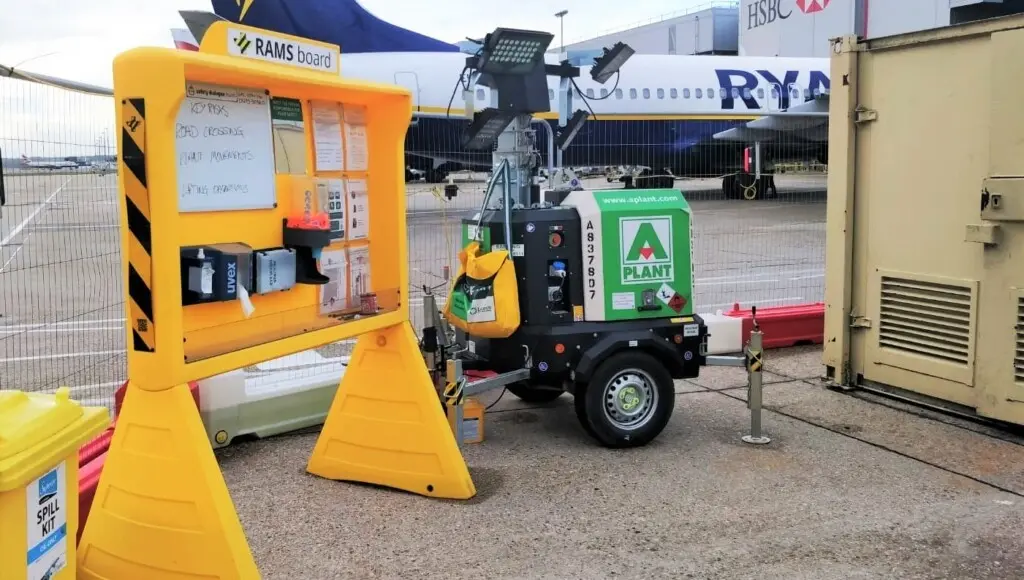
To resolve these issues, the company implemented RAMS Boards, which offered weather-resistant document holders, fire safety integration, and spill kit options. The boards were relocated easily as work zones shifted, ensuring that workers always had access to current safety information.
Regulatory inspectors praised the improved document organization, which simplified audits. Worker engagement also increased, with fewer incidents related to unclear safety protocols.
2. Case Study: Fire Safety Solutions on a High-Risk Construction Site
A construction site for a high-rise building was classified as high-risk due to the presence of flammable materials and ongoing welding operations. The site management team needed a robust solution to manage fire safety. They partnered with Howler SafetyHub, which provided fire alarm points and integrated fire extinguishers at key locations.
The safety hubs were equipped with manual push-button alarms that allowed workers to quickly activate site-wide alerts during fire incidents. Weekly fire drills and system checks were scheduled to ensure preparedness.
Emergency response times improved significantly, and the site passed multiple safety inspections without any major deficiencies. The safety team credited the centralized system for improving visibility and accessibility of fire safety tools.
3. Lessons Learned from Real-World Applications
These case studies demonstrate that centralized safety hubs offer significant benefits, including:
Lesson Learned | Details |
---|---|
Improved Compliance | Centralized safety hubs organize and protect safety documents, reducing the likelihood of regulatory violations during inspections. |
Enhanced Emergency Response | Integrated emergency tools, such as fire alarms, spill kits, and first aid stations, allow for faster, more coordinated responses to on-site emergencies. |
Increased Worker Engagement | Consistent access to current safety information raises worker awareness, encouraging better adherence to safety protocols and procedures. |
Operational Efficiency | Automating reminders for inspections, document updates, and safety drills minimizes administrative workloads and improves site operations. |
Spill Kit Integration | Safety hubs with spill kits provide immediate resources to contain and clean hazardous spills, reducing environmental risks and improving incident control. |
Reduced Communication Delays | Safety hubs ensure that crucial updates on hazards, schedules, and weather conditions are immediately available to workers, promoting faster responses. |
Sustainability Improvements | Durable materials and reusable designs help reduce waste and environmental impact, aligning with sustainability goals. |
Increased Hazard Visibility | Clear layouts and document displays ensure critical safety notices, emergency routes, and hazard symbols remain highly visible to workers and visitors. |
Elevating Site Safety with Centralized Hubs
In today’s fast-paced and high-risk construction environments, ensuring worker safety and regulatory compliance is a complex, yet essential, task. Centralized safety hubs have become a crucial tool for site managers and heads of safety, providing a structured, adaptable platform for safety communication, emergency preparedness, and compliance management. Platforms like RAMS Boards and Howler SafetyHub are leading the way in transforming how safety information is delivered, accessed, and updated on worksites.
These hubs consolidate multiple safety functions, offering features such as fire safety points, spill kit integration, and digital updates. Their modular design, portability, and customizability make them adaptable to various industries and projects. By addressing common challenges related to information accessibility, worker engagement, and document management, construction safety hubs help reduce risks and foster a proactive safety culture.
Summary of Key Benefits
The adoption of construction safety hubs provides several critical benefits:
- Improved Compliance Management: Centralized platforms organize safety documentation, making it easy for site managers to meet regulatory requirements and pass inspections. Automated reminders and notifications help prevent compliance oversights.
- Enhanced Emergency Preparedness: Integrated emergency tools, such as fire alarms and spill kits, ensure that workers can respond quickly to incidents. Real-time updates improve coordination during emergencies, reducing response times and injury risks.
- Dynamic Safety Communication: Platforms offer tools for real-time updates, such as magnetic whiteboards and digital alerts. Workers remain informed of evolving hazards and procedures, supporting continuous risk management.
- Customization for Industry Needs: Safety hubs can be tailored to include features specific to each project’s risks, such as fire safety protocols, equipment permits, or hazardous material handling. This flexibility helps companies meet unique site requirements.
- Worker Engagement and Accountability: By providing clear, organized, and regularly updated safety information, hubs encourage workers to take responsibility for their actions. Behavioral prompts and motivational messaging further reinforce a culture of safety awareness.
Warren Alexander-Pye Associate Director: “We have bought two RAMS boards for a very challenging site environment below a London Underground station.
The robust construction of the boards means they can withstand the rigours of site, they are easily cleaned and the ability to drain the base units makes them easy to move as the works phases progress.
Where the method statement is highly bespoke and out of the ordinary these boards are great for ensuring the relevant information is available close to the workface.
The cost compares very favourably with the site made timber version, the range of pre-fixed accessories available is very good and the fact that we could brand the sign on top of the board was the icing on the cake.
I would recommend these to any site.”
(Google reviews) Fred Peck: “The quality of the materials is top-notch. You can tell, RAMS boards are built to last.”
Looking Ahead: Adopting Modern Safety Solutions
The construction industry is undergoing significant transformation with the integration of technology and sustainability in safety management. Companies that adopt modern safety hubs will be better equipped to handle the increasing complexity of safety regulations and the growing focus on sustainability. Future trends such as IoT integration, augmented reality (AR), and advanced data analytics will further enhance safety performance, giving site managers new tools to identify risks and improve worker protection.
Sustainability initiatives will also play a larger role. Platforms like RAMS Boards, which use eco-friendly materials such as recycled HDPE, set an example for reducing the environmental impact of safety infrastructure. As businesses prioritize sustainability, modular, reusable safety hubs will become a standard part of construction operations.
For construction professionals, adopting a centralized safety hub is no longer optional—it is essential for maintaining compliance, protecting workers, and improving operational efficiency. Site managers and heads of safety are encouraged to evaluate their current safety communication infrastructure and consider modern platforms that offer enhanced features and customization.
Whether managing a large infrastructure project, a chemical manufacturing plant, or a logistics center, the benefits of safety hubs are clear. Companies that invest in these solutions will not only reduce accidents and liabilities but also build a reputation for safety excellence, positioning themselves as leaders in their industry.
By taking proactive steps today, you can elevate your site safety standards and ensure a safer, more compliant future for your workforce.
What is a construction safety hub, and how does it improve site safety?
A construction safety hub is a centralized platform designed to manage and communicate safety protocols on construction sites. It consolidates critical safety information, such as risk assessments, emergency procedures, and hazard alerts. Modern hubs like RAMS Boards and Howler SafetyHub also integrate emergency equipment (e.g., fire alarms, spill kits), making safety communication more efficient and ensuring quick access to vital tools during emergencies.
What kinds of safety information are typically displayed on a safety hub?
Safety hubs display a wide range of information essential for maintaining compliance and worker safety, including: Risk assessments and method statements (RAMS) Fire safety procedures and evacuation routes Emergency contacts and first aid information Hazard alerts for ongoing risks on-site Inspection schedules and permits These features ensure that workers have access to up-to-date safety guidance at all times.
How do safety hubs help with regulatory compliance?
Safety hubs help streamline compliance by organizing key safety documents in one central location. Platforms offer transparent document holders for risk assessments, permits, and inspection records, which are protected from environmental damage. Automated notifications for inspection dates and permit renewals also help site managers stay on top of regulatory requirements. During audits, inspectors can easily verify compliance by reviewing the information displayed on the hub.
What customization options are available for safety hubs?
Safety hubs can be tailored to meet the specific needs of each project or industry. Customization options include: Integration of fire safety points, spill kits, and first aid stations Custom layouts for displaying site-specific hazards and emergency plans Company branding, including logos and motivational messaging Digital tools, such as QR codes and mobile alerts, for accessing documents and updates These features improve both safety communication and worker engagement.
How do safety hubs improve emergency preparedness on construction sites?
Safety hubs enhance emergency preparedness by integrating essential tools and providing real-time access to safety protocols. Features such as fire alarms, evacuation maps, and spill kits are positioned for quick access. Platforms like Howler SafetyHub offer site-wide alarm systems, while RAMS Boards allow for customizable emergency tool integration. These capabilities reduce response times and improve coordination during incidents.
What future trends are shaping the development of construction safety hubs?
Sustainability: Use of eco-friendly materials, such as recycled HDPE, and modular designs for reusability. Advanced Analytics: Platforms that analyze safety performance data to identify risks and improve decision-making. These innovations are making safety management more adaptive, data-driven, and environmentally responsible.