Construction sites are often chaotic and unpredictable, making safety a top priority. Among the many safety measures, eye wash stations stand out as essential lifesaving equipment. These stations are not just about compliance with regulations; they play a critical role in protecting workers from the dangers of hazardous substances and airborne debris. Designed for immediate eye irrigation, they serve as a vital defense against chemical splashes and flying particles—common hazards in construction environments.
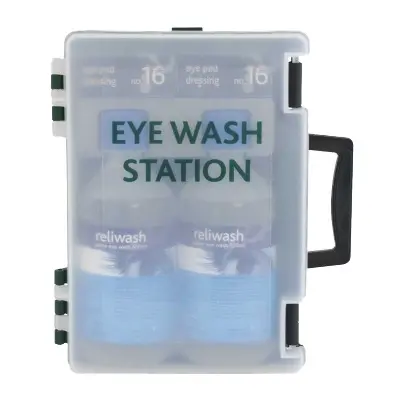
Consider this scenario: a worker is exposed to a splash of corrosive chemicals or a dense cloud of dust from a cutting tool. In such moments, having an eye wash station nearby can turn a potentially catastrophic situation into a manageable one. These stations are engineered for swift and effective action, providing immediate relief and significantly reducing the risk of long-term eye damage.
As construction sites continue to adopt cutting-edge materials and technologies, the importance of eye wash stations becomes even more pronounced. These stations are more than just functional equipment; they symbolize the industry’s commitment to worker safety and health. By installing eye wash stations, companies demonstrate that the well-being of their workforce is a top priority.
Looking ahead, one might ask: what’s next for eye wash stations? Could advancements in technology make them smarter, more user-friendly, or even more efficient? The possibilities are vast, reflecting the construction industry’s ongoing drive to innovate and protect its people.
Importance of Eye Wash Stations in Construction
Construction sites are inherently unpredictable and often hazardous, making worker safety a top priority. Among the many safety measures, eye wash stations are indispensable. These stations are not just regulatory requirements—they are lifesaving tools designed to address eye injury risks from construction hazards, forming a critical pillar of workplace safety.
Consider the dangers present in construction environments: chemical splashes, airborne dust, and flying debris are just a few of the common threats to workers’ eyes. If left unaddressed, these hazards can lead to severe injuries. This is where eye wash stations play a vital role. They provide immediate relief, acting as the first line of defense and significantly reducing the risk of long-term damage.
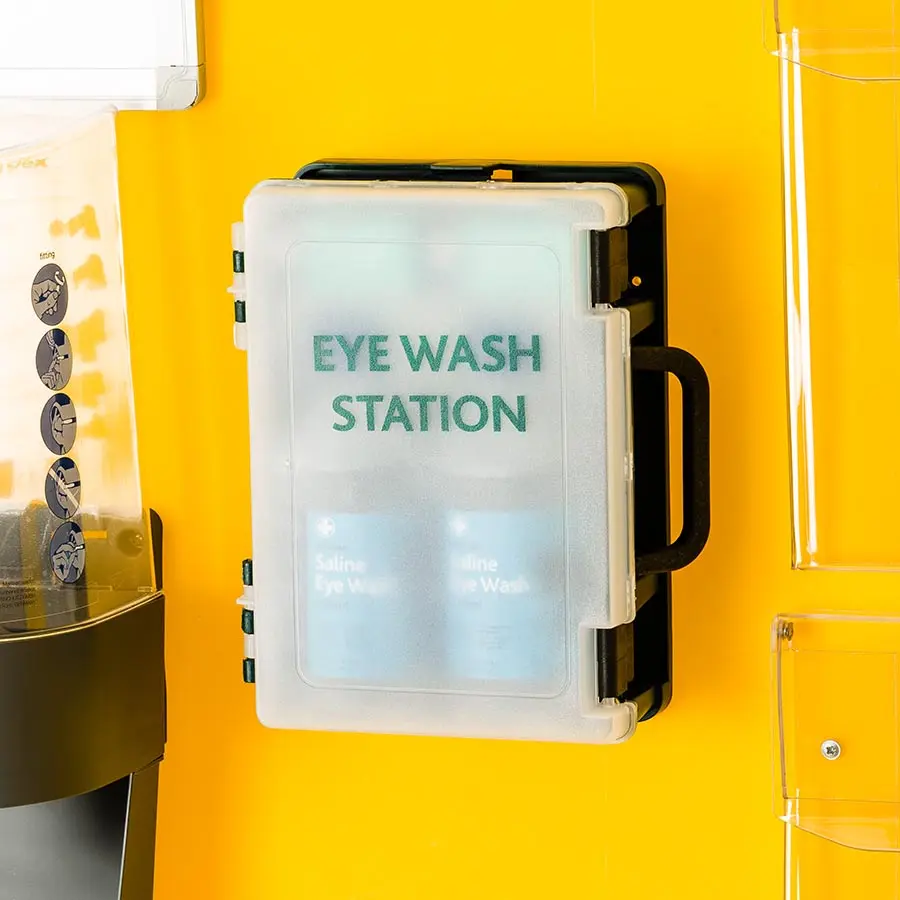
However, their effectiveness depends on proper planning. Conducting thorough risk assessments is essential to identify potential threats and guide the strategic placement of eye wash stations. Proper positioning ensures workers can access them quickly during emergencies, making a tangible difference in workplace safety.
As construction techniques evolve, the role of eye wash stations becomes even more critical. They symbolize the industry’s commitment to safety and proactive worker protection. Looking ahead, one can envision how emerging safety technologies might enhance these stations, making them even more efficient and accessible.
Common Hazards Requiring Eye Wash Stations
Construction sites are rife with risks, particularly for workers’ eyes. Among the most common hazards are:
- Chemical splashes: Exposure to corrosive or harmful chemicals can cause immediate and severe eye damage.
- Airborne dust: Dust from cutting, grinding, or drilling operations can irritate or injure the eyes.
- Flying debris: Particles from construction activities can strike the eyes, leading to potential injuries.
Without immediate intervention, these threats can result in serious injuries, underscoring the non-negotiable need for accessible eye wash stations. Imagine a worker splashed with a corrosive chemical or engulfed in a cloud of dust. In those critical moments, an eye wash station can mean the difference between a minor scare and a life-altering injury. These stations are engineered to deliver fast, effective relief, helping to prevent lasting damage.
The connection between construction hazards and eye wash stations is undeniable. These stations act as a safety net, shielding workers from daily dangers. As construction sites adopt innovative materials and technologies, the importance of eye wash stations only grows. They stand as a testament to the industry’s steadfast dedication to worker safety.
Looking to the future, it’s exciting to imagine how technology might revolutionize eye wash stations. Could we see designs that are more intuitive and efficient? The possibilities are endless, reflecting the industry’s relentless pursuit of innovation and safety.
Role of Eye Wash Stations in Workplace Safety
In the realm of workplace safety, eye wash stations are transformative, particularly in high-risk settings like construction sites. They go beyond compliance, ensuring workers have immediate access to eye irrigation when exposed to harmful substances or particles.
Risk assessments play a pivotal role in maximizing the effectiveness of these stations. By identifying specific hazards, these evaluations determine the optimal placement of eye wash stations for maximum impact. This proactive strategy minimizes the likelihood of severe eye injuries and underscores the value of well-planned safety measures.
The synergy between eye wash stations and risk assessments is clear. While the stations provide critical emergency care, the assessments ensure they are strategically located where they are needed most. This collaboration enhances overall workplace safety, offering workers peace of mind and preparedness for emergencies.
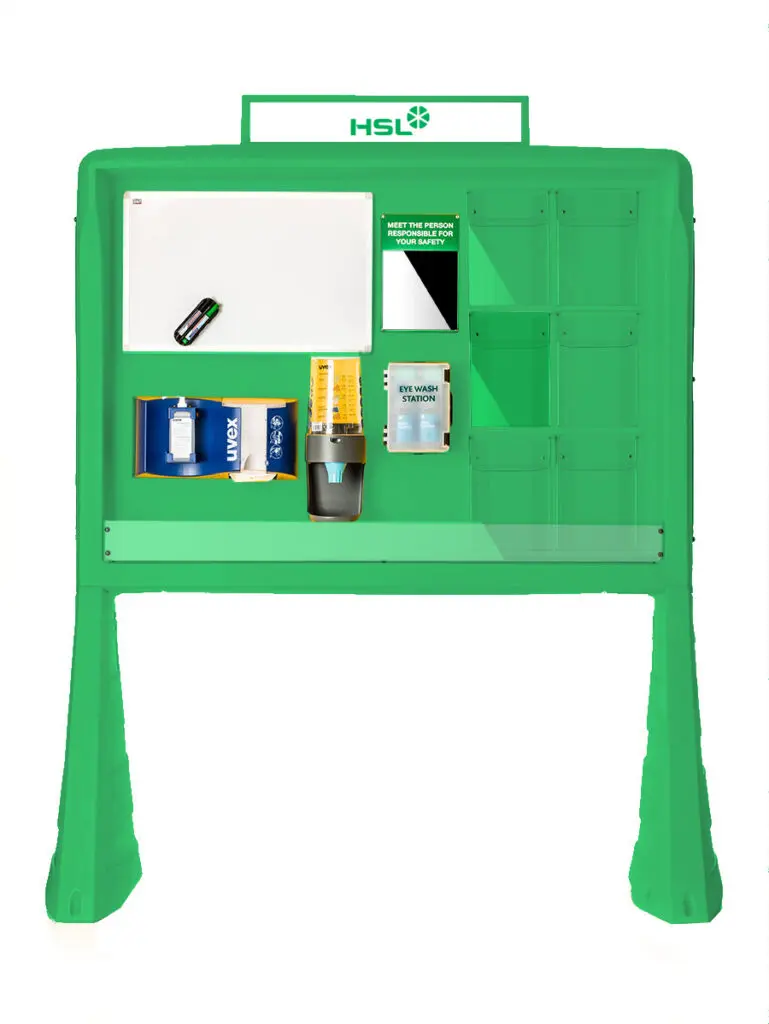
As safety standards evolve, there is always room for improvement. How can risk assessment processes be refined to offer even greater protection? What innovative strategies could make eye wash stations more effective? These questions drive the ongoing pursuit of higher safety standards and better practices, ensuring that workers remain protected in ever-changing environments.
Types of Eye Wash Stations for Construction Sites
Construction sites are bustling hubs of activity, where safety must always take precedence. Choosing the right eye wash station can be a game-changer when emergencies arise. With various types available, each tailored to specific hazards and conditions, understanding your options is essential for safeguarding workers and adhering to safety standards.
Here are the main types of eye wash stations:
- Portable Eye Wash Stations: Compact and self-contained, these units are indispensable in areas lacking a fixed water supply. They’re ideal for remote or temporary locations, providing immediate eye irrigation when it’s needed most.
- Plumbed-In Eye Wash Stations: Permanent installations connected to a water source, delivering a continuous flow of water. These are perfect for high-risk zones where severe eye injuries are more likely.
- Combination Eye/Face Wash Stations: Designed to flush both the eyes and face, ensuring thorough decontamination in areas prone to chemical splashes or heavy dust.
- Personal Eye Wash Bottles: Portable, quick-relief tools that provide sterile saline irrigation until a more robust solution is accessible.
Together, these options form a safety net tailored to the unique challenges of construction sites. With technology advancing rapidly, one can’t help but wonder: how might future innovations transform these eye wash stations? Could we see smarter, more adaptive safety solutions that redefine workplace safety?
Portable Eye Wash Stations: Features and Benefits
Portable eye wash stations are a cornerstone of safety for construction sites, particularly those without access to a fixed water supply. Designed for immediate eye irrigation, they address injuries caused by dust, debris, or chemical splashes. Their mobility allows them to be strategically placed across a site, ensuring they’re always within reach.
Key features and benefits of portable eye wash stations include:
- Versatility: Ideal for remote or temporary locations where traditional plumbed-in stations aren’t feasible.
- Durability: Models like the Hughes STD-40K range are built tough to withstand rugged construction site conditions.
- Adaptability: Perfect for projects that are constantly evolving, ensuring safety measures keep pace with changing needs.
As construction projects grow more intricate, the need for flexible safety solutions like portable eye wash stations will only increase. Who knows? Future innovations might make these units even more efficient and user-friendly, solidifying their role in workplace safety.
Plumbed-In Eye Wash Stations: When to Use Them
Plumbed-in eye wash stations are a mainstay in areas where the risk of severe eye injuries is significant. These fixed units connect directly to a water supply, providing a steady stream of water to flush out irritants during emergencies. They’re a dependable, always-available solution for workers in need.
Advantages of plumbed-in eye wash stations include:
- Consistent Performance: Ensures compliance with stringent safety standards, such as EN 15154-2.
- Reliability: Always available for immediate use, making them indispensable in high-risk environments.
- Suitability for Hazardous Areas: Ideal for environments where hazardous materials are frequently handled.
As safety technology continues to evolve, it’s intriguing to consider how advancements in plumbing and design might enhance these stations. Could we see more adaptable, efficient models tailored to the dynamic needs of modern construction sites? The possibilities are endless.
Combination Eye/Face Wash Stations for High-Risk Areas
In high-risk environments—think chemical splashes or heavy dust exposure—combination eye/face wash stations are indispensable. These units are designed to flush both the eyes and face, providing comprehensive decontamination when workers encounter hazardous substances. This dual functionality is critical for minimizing injuries and accelerating recovery.
Key benefits of combination eye/face wash stations include:
- Comprehensive Decontamination: Flushes both the eyes and face, ensuring thorough cleaning of hazardous substances.
- Integration with Safety Showers: Often paired with safety showers to form a complete decontamination system.
- Rapid Response: Provides swift and effective treatment, crucial in areas with high exposure risks.
As construction sites evolve, it’s worth speculating: how might these stations adapt to meet growing safety demands? Could future designs become more compact, intuitive, and efficient, making them an even better fit for high-risk areas?
Personal Eye Wash Bottles: Temporary Solutions
Personal eye wash bottles are a straightforward yet highly effective first aid tool, offering immediate relief in the event of an eye injury. Filled with sterile saline solution, these bottles are easy to use and provide a quick, temporary fix until a more comprehensive eye wash station is accessible. Their portability ensures they’re always within arm’s reach during emergencies.
Why personal eye wash bottles are essential:
- Immediate Relief: Delivers instant irrigation to mitigate the severity of injuries.
- Portability: Easy to carry and always within reach during emergencies.
- Temporary Solution: Buys crucial time for workers to reach a permanent eye wash station.
As the construction industry continues to prioritize safety, it’s exciting to imagine how personal eye wash solutions might evolve. Could innovations in design or delivery systems make these bottles even more effective and user-friendly? The future holds promise for these essential safety tools.
RAMS eye wash boards: a comprehensive first aid station
RAMS boards, made of high-density polyethylene (HDPE), can include an integrated eyewash station, transforming them into a comprehensive first aid hub in the workplace. The integration of an eyewash station enhances emergency preparedness by providing immediate access to critical first aid supplies. These stations typically include securely mounted saline bottles, eye dressings, and sterile wash solutions, positioned for easy retrieval in high-risk environments. The design ensures that all emergency materials remain organized and easily accessible, minimizing response time in case of eye contamination from dust, chemicals, or debris.
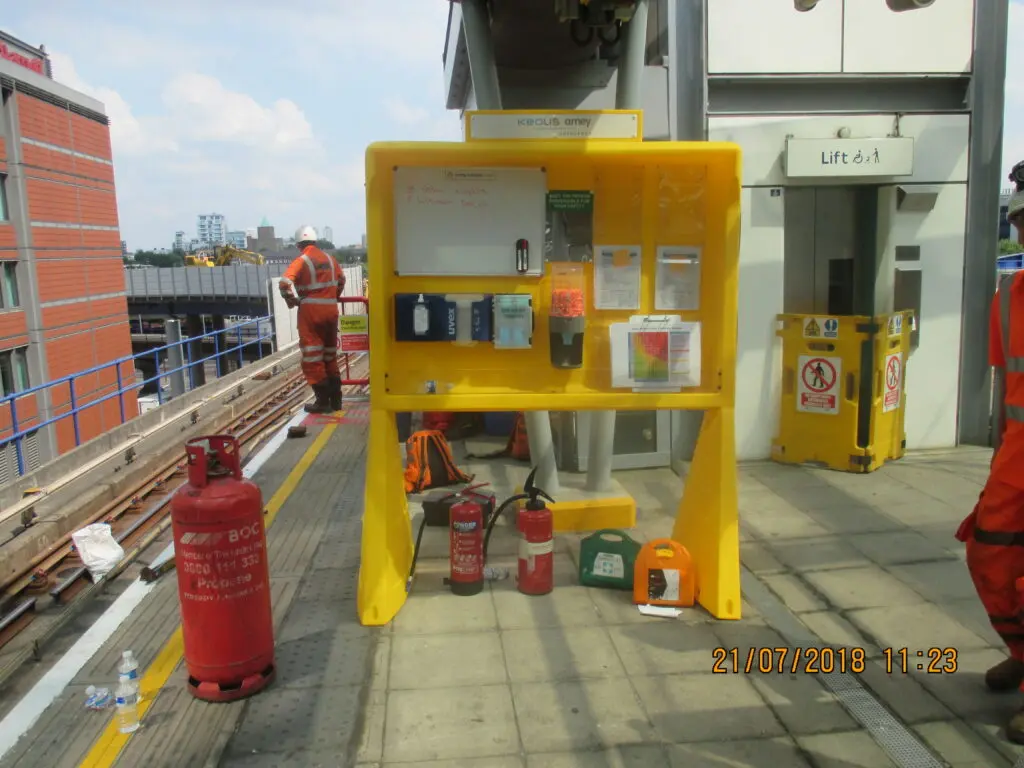
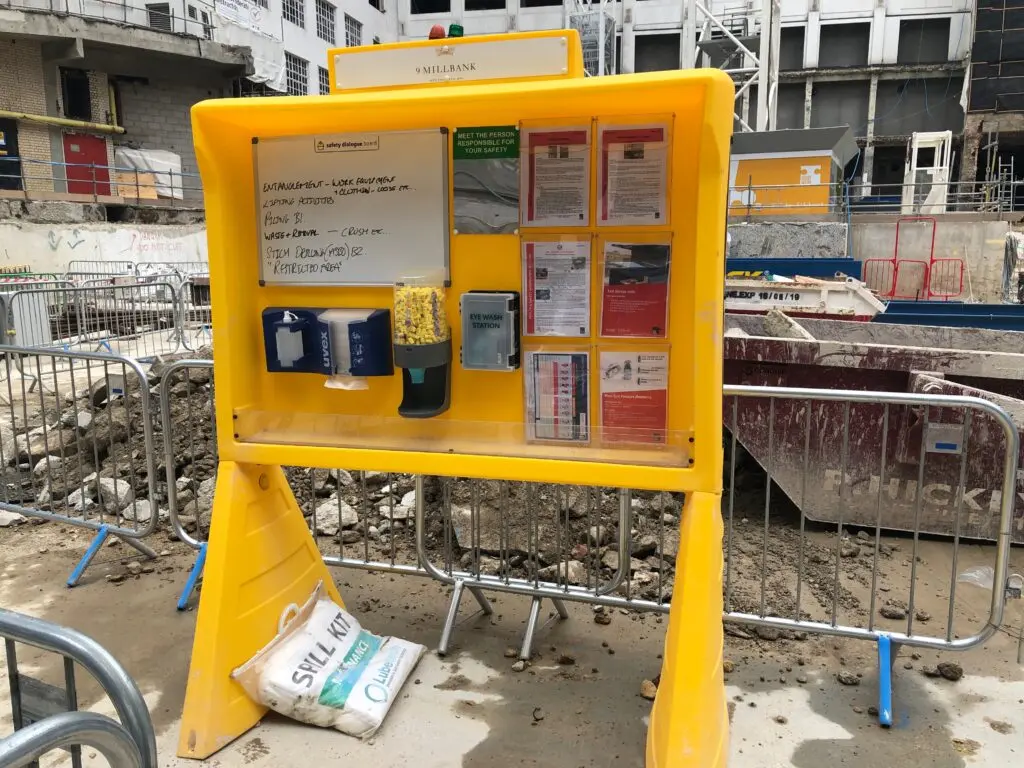
In accordance with Health & Safety Executive (HSE) guidelines, RAMS boards equipped with an eyewash station support workplace safety standards, reducing the risk of prolonged exposure to hazardous substances. The inclusion of clearly labeled emergency instructions and high-visibility signage further streamlines the response process, ensuring employees can take swift action even in high-stress situations.
Standards and Regulations for Eye Wash Stations
Workplace safety—especially on construction sites—demands strict adherence to eye wash regulations. These rules are not merely guidelines; they are essential safeguards ensuring that eye wash stations are present, fully operational, and ready to provide immediate care during emergencies. Compliance with these standards is critical to protect workers from eye injuries caused by hazardous materials or flying debris.
Understanding these specific requirements empowers construction site managers to implement robust safety measures. By meeting these standards, they ensure that eye wash stations are both safe and functional, fostering a more secure environment for everyone on site.
ANSI Z358.1-2014(R2020): Key Requirements
The globally recognized ANSI Z358.1-2014(R2020) standard sets the benchmark for the installation and performance of eye wash and safety shower equipment. This comprehensive guideline outlines critical details, such as flow rates and accessibility features, that eye wash stations must meet to remain compliant. Adhering to these standards ensures that emergency equipment will function effectively when it’s needed most.
- Flow Rate: A key focus of the ANSI standard, ensuring sufficient water is available to flush out harmful substances quickly during emergencies.
- Accessibility: Eye wash stations must be easily reachable within 10 seconds of an incident, ensuring immediate response.
- Temperature Control: Water temperature should be tepid (60-100°F) to prevent further injury during use.
By adhering to these requirements, workplaces can minimize the risk of long-term damage caused by hazardous exposure and ensure compliance with global safety standards.
EN 15154-2: European Standards for Plumbed-In Stations
In Europe, the EN 15154-2 standard defines the essential requirements for plumbed-in eye wash stations and emergency showers. This regulation ensures that these stations provide a reliable and safe method for decontamination when workers are exposed to hazardous substances.
- Plumbed-In Design: Stations must be connected to a reliable water source to ensure consistent functionality.
- Flow Rate and Duration: The system must deliver a continuous flow of water for at least 15 minutes.
- Accessibility: Stations should be located in areas where hazardous materials are handled, ensuring quick access during emergencies.
Compliance with EN 15154-2 is particularly critical for sites handling chemicals or other dangerous materials. By following these guidelines, companies can ensure their eye wash stations are prepared for emergencies, safeguarding their teams and maintaining exemplary safety standards.
OSHA and HSE Guidelines for Eye Wash Stations
Both OSHA (Occupational Safety and Health Administration) and HSE (Health and Safety Executive) have established emergency eyewash requirements that serve as a blueprint for the installation and upkeep of eye wash stations. These guidelines are indispensable for maintaining safety in high-risk environments like construction sites.
- Regular Maintenance: Eye wash stations must be inspected and tested weekly to ensure they remain fully functional.
- Accessibility: Stations should be unobstructed and reachable within 10 seconds of an incident.
- Training: Workers must be trained on the proper use of eye wash stations to ensure effective responses during emergencies.
- Record-Keeping: Maintenance logs should be kept to document inspections and repairs.
As safety standards evolve, one question lingers: what innovations lie ahead? Could future regulations introduce advanced technologies like automated monitoring systems or state-of-the-art decontamination methods? These advancements might redefine workplace safety, setting a new standard for emergency preparedness.
Placement and Accessibility of Eye Wash Stations
The location and ease of access to eye wash stations can mean the difference between a minor incident and a major emergency. Imagine a bustling construction site where every second counts if hazardous materials come into contact with someone’s eyes. For this reason, these stations must be strategically placed in areas where workers can reach them without delay—especially in zones where dangerous substances are frequently handled. Safety guidelines recommend that eye wash stations be no more than a 10-second sprint away from any potential hazard. This proximity ensures workers can respond swiftly when urgency strikes.
Accessibility, however, goes beyond proximity. It also involves ensuring the path to the station is clear and unobstructed. Picture rushing to an eye wash station only to trip over scattered tools or debris—that’s a recipe for disaster. Keeping access routes free of obstacles is just as critical as the station’s placement. By prioritizing smart positioning and maintaining clutter-free pathways, construction sites can significantly enhance safety measures, equipping workers with the resources they need to safeguard their vision in those crucial moments.
Barrier-Free Eye Wash Stations for Inclusive Safety
Barrier-free eye wash stations represent a transformative step toward making construction sites safer for everyone. These stations are designed with inclusivity at their core, ensuring that workers with disabilities have the same quick access to emergency eye care as their colleagues. In high-risk environments like construction, this accessibility can be the difference between a minor scare and a life-altering injury.
Barrier-free designs often include user-friendly features such as lower activation controls and wide, unobstructed pathways, making them accessible to workers in wheelchairs or those with limited mobility. By adopting these inclusive designs, construction sites not only comply with accessibility standards but also demonstrate a genuine commitment to the well-being of their entire workforce. This approach goes beyond meeting regulations—it fosters a workplace where every individual feels valued and protected. Inclusive safety measures don’t just enhance protection; they build a stronger, more equitable environment for all.
Maintenance and Inspection of Eye Wash Stations
Maintaining eyewash stations in excellent condition is crucial for safeguarding workers’ health and safety on construction sites. Imagine the consequences if these vital devices fail during a critical moment. That’s a risk no one should take. By performing weekly inspections, potential issues can be identified and resolved promptly, ensuring these stations are always ready to act in emergencies.
These inspections are more than just a compliance requirement—they are a proactive measure to protect workers from hazardous substances. Incorporating regular maintenance into your safety routine not only minimizes the risk of eye injuries but also fosters a safer and more secure work environment for everyone.
As technology evolves, innovative tools could simplify the upkeep of these stations. Picture automated systems that transform safety protocols and redefine reliability standards altogether. Could these advancements revolutionize how we maintain eyewash stations?
Weekly Inspection Procedures
When it comes to eyewash station inspections, weekly checkups are indispensable. These evaluations ensure that every component functions as intended. The process includes:
- Activating the stations to verify proper operation.
- Checking for obstructions that could hinder accessibility.
- Confirming water flow meets required standards.
This straightforward routine ensures the stations are always prepared to provide immediate relief in case of an eye injury.
However, weekly inspections are just one part of a comprehensive maintenance strategy. Regular cleaning and performance testing are equally important. By adhering to these practices, you’re not just complying with safety regulations—you’re ensuring that your eyewash stations are genuinely effective when they’re needed most.
Looking ahead, digital advancements could revolutionize this process. Imagine real-time monitoring systems that instantly alert you to any issues. Could these innovations make weekly inspections quicker, simpler, and even more dependable?
Ensuring Proper Functionality and Compliance
Ensuring an eyewash station is in optimal working condition isn’t optional—it’s essential for protecting workers on construction sites. This involves a commitment to:
- Regular cleaning to maintain hygiene and functionality.
- Detailed inspections to identify and address potential issues.
- Rigorous testing to confirm the stations meet all safety standards.
Such diligence provides peace of mind, knowing these devices are ready to deliver critical eye irrigation during emergencies.
Compliance is about more than just following rules—it’s a testament to prioritizing worker safety above all else. By maintaining eyewash stations to the highest standards, you’re not only reducing the likelihood of eye injuries but also cultivating a culture of safety that everyone can trust.
As we look to the future, it’s exciting to imagine how technology could enhance this process. Could emerging innovations streamline compliance and maintenance? Perhaps they’ll help us set even higher benchmarks for safety on construction sites.
Specialized Eye Wash Solutions for Construction Sites
Construction sites are inherently unpredictable when it comes to safety. In these high-risk environments, having the right eye wash solutions is not just a precaution—it’s an absolute necessity. Products like sterile saline and neutralizing agents act as critical lifesavers. They work swiftly to flush out harmful substances, providing immediate relief and significantly reducing the risk of severe injuries. Think of them as the emergency responders for your eyes, stepping in when every second counts.
For site managers, selecting the right eye wash solution is a crucial responsibility. It demands a thorough understanding of the specific hazards—whether it’s chemical splashes, airborne dust, or flying debris. Tailoring eye wash stations to address the unique risks of your site goes beyond mere compliance; it’s about creating a safer, more secure environment for every team member.
As construction sites evolve with cutting-edge technology and new challenges, one question looms large: how will eye wash solutions adapt? Could future innovations bring smarter, faster, and more efficient ways to safeguard workers’ vision? It’s a fascinating topic that deserves attention as the industry progresses.
Portable Eye Wash with Heated Jackets for Cold Environments
Working in freezing temperatures presents a unique set of challenges, especially when it comes to safety equipment. Portable eye wash stations with heated jackets offer a groundbreaking solution for these frosty conditions. These systems are designed to maintain water at an optimal temperature, ensuring it’s always ready for effective eye irrigation. No frozen water. No compromised performance. Just reliable safety when it’s needed most.
Beyond keeping the water warm, these heated jackets ensure compliance with eyewash standards. This eliminates the discomfort of icy water and guarantees a process that is both effective and regulation-friendly. For construction sites operating in extreme weather, this innovation is indispensable for maintaining safety and meeting industry standards.
As projects increasingly venture into harsher climates, it’s worth considering: how will portable eye wash stations evolve to meet these demands? Could future designs become even more robust and versatile, capable of withstanding the harshest conditions? The possibilities are as vast as the challenges ahead.
Eye Wash Solutions: Sterile Saline and Neutralizing Agents
When it comes to protecting workers’ vision, the right eye wash solutions are absolutely essential. Sterile saline and neutralizing agents stand out as top-tier options, designed to rapidly flush out harmful substances and minimize the risk of lasting damage. They serve as the first line of defense in emergencies, delivering immediate relief when every moment matters.
The choice of solution depends on the specific hazards present. Sterile saline is ideal for general eye irrigation, while neutralizing agents are critical in environments with significant chemical risks. By equipping your eye wash stations with the appropriate tools, you empower your team to handle a wide range of potential incidents with confidence and efficiency.
As safety remains a top priority in the construction industry, one pressing question arises: how will advancements in eye wash formulations redefine protection? Could we see solutions that offer unparalleled defense against an even broader spectrum of hazards? While the future is uncertain, it holds immense promise for innovation and enhanced safety.
Enhancing Safety with Additional Features
Ensuring worker safety on construction sites is a challenging task that requires constant innovation and meticulous attention to detail. Among the many safety measures available, eye wash station signage stands out as a critical component. Why? Because in emergencies, every second counts. Clear and highly visible signs can mean the difference between swift action and delayed response, guiding workers to eye wash stations precisely when they need them most.
Another transformative safety measure is the implementation of combination safety showers. These versatile units integrate eye wash stations with body showers, creating an all-in-one decontamination solution. In workplaces where hazardous materials are a daily reality, this dual-purpose setup is indispensable. By addressing both eye and body safety, combination showers elevate workplace protection, ensuring teams are prepared for virtually any scenario.
Looking ahead, the future of safety innovations is promising. Imagine emergency response systems equipped with cutting-edge designs or advanced technologies that make them faster and more efficient. The possibilities are as exciting as they are essential for improving workplace safety.
Eye Wash Station Signage for Quick Identification
Construction sites are often chaotic, and in such environments, locating safety equipment quickly can mean the difference between a minor incident and a severe injury. This is where eye wash station signage becomes invaluable. These signs act as beacons, directing workers to essential safety gear when every moment matters. Their role in maintaining workplace safety cannot be overstated.
However, visibility alone is not enough. Signs must be strategically positioned and easy to understand. Placing them at eye level in well-lit, high-traffic areas ensures they are impossible to miss. This thoughtful placement not only minimizes risks but also instills confidence in workers, knowing that help is always within reach.
The future of safety signage holds exciting potential. Imagine digital signs that illuminate or adapt dynamically to changing site conditions. These advanced solutions could redefine safety standards on construction sites, making them safer and more efficient than ever before.
Combination Safety Showers for Comprehensive Decontamination
In workplaces where hazardous materials are part of daily operations, having combination safety showers readily available is non-negotiable. These robust units combine eye wash stations with body showers, offering a comprehensive decontamination solution in one compact system. Whether it’s a chemical spill or exposure to airborne contaminants, this dual functionality empowers workers to respond quickly and effectively.
Beyond their practicality, these showers send a powerful message: worker safety is a top priority. By providing thorough rinsing for both eyes and the body, they help prevent long-term injuries, accelerate recovery, and maintain operational efficiency. It’s a win-win scenario for both employees and employers.
As safety protocols continue to evolve, so too do the tools we rely on. Future iterations of these showers could feature sleek, ergonomic designs or even smart technology that enhances usability in high-stress situations. The potential for innovation in this area is vast, and it’s thrilling to imagine what lies ahead for workplace safety.
Conducting Risk Assessments for Eye Wash Stations
Ensuring safety on construction sites begins with comprehensive risk assessments for eye wash stations. These evaluations are crucial for identifying where stations are most needed and integrating them into the overall safety framework. By analyzing site-specific hazards—such as chemical splashes, airborne debris, or dust—these assessments provide a clear roadmap for implementing essential safety measures.
However, risk assessments go beyond merely identifying hazards. They evaluate the severity and likelihood of potential risks, shaping decisions about the type, quantity, and placement of eye wash stations. For example:
- A site handling hazardous chemicals may require multiple plumbed-in stations near high-risk zones.
- A dusty environment might benefit from strategically placed portable units.
This tailored approach ensures that stations are positioned where they are needed most, enhancing both safety and preparedness.
As construction practices evolve, one critical question arises: how might emerging technologies reshape risk assessments? Could real-time digital tools revolutionize hazard analysis, making the placement of eye wash stations more adaptive and precise?
Evaluating Construction Site Hazards
Understanding construction site hazards is fundamental to determining the optimal placement of eye wash stations. Construction sites are inherently dangerous, with risks such as chemical splashes and airborne particles posing significant threats to workers’ eye health. Detailed hazard evaluations enable site managers to pinpoint the most critical areas for station placement, ensuring workers have immediate access to emergency eye irrigation when needed.
The connection between workplace hazards and eye wash stations is clear. These stations act as the first line of defense against eye injuries, mitigating the effects of common construction risks. For instance:
- Zones where corrosive chemicals are frequently used may require plumbed-in stations with continuous water flow.
- Less hazardous areas could rely on portable units for flexibility and convenience.
Customizing safety measures to address specific risks fosters a safer and more responsive work environment.
As safety remains a top priority, it’s worth considering: how can advanced technologies enhance hazard evaluations? Could AI-powered detection systems pave the way for smarter, more accurate placement of eye wash stations, setting new benchmarks for workplace safety?
Determining the Right Type and Placement of Stations
Choosing the appropriate type and location for eye wash stations requires meticulous planning and a thorough understanding of workplace hazards. Risk assessments serve as the foundation of this process, enabling site managers to address the unique safety demands of their environment. For example:
- A site with frequent chemical exposure might necessitate plumbed-in stations for continuous water flow.
- A more dynamic worksite could benefit from portable or combination units for greater flexibility.
Equally important is the strategic placement of these stations. Their effectiveness depends on how quickly they can be accessed during an emergency. Risk assessments highlight high-risk zones, guiding site managers to position stations within seconds of potential hazards. This proactive strategy not only enhances worker safety but also ensures compliance with stringent safety regulations. For instance, placing a station near a chemical storage area or a zone prone to dust clouds can significantly reduce response times in urgent situations.
As construction sites become increasingly complex, the future holds exciting possibilities: could predictive modeling and advanced hazard analysis tools refine these decisions even further? Imagine systems that anticipate risks and dynamically adjust the placement of safety equipment, setting a new gold standard for workplace safety.
Training and Best Practices for Eye Wash Station Use
Picture a bustling construction site, where hazards lurk around every corner. In such environments, knowing how to use eye wash stations isn’t just about compliance—it’s about saving lives. When workers are equipped with the knowledge to act swiftly and decisively during emergencies, they can prevent minor mishaps from escalating into serious injuries. Regular eyewash station training instills confidence, arming workers with the skills they need to respond effectively when every second matters.
Effective training programs should begin with the essentials:
- Pinpointing the locations of eye wash stations.
- Understanding their operation and how to activate them.
- Grasping the urgency of immediate action in the event of an eye injury.
Workers must master the step-by-step process, from activating the system to adhering to the critical 15-minute flushing guideline. By embedding this training into the daily routine, construction sites can foster a safety-first mindset, ensuring everyone is ready to act swiftly and wisely in emergencies.
But here’s an intriguing idea—what if cutting-edge technology could elevate training to new heights? Imagine leveraging virtual reality or interactive tools to recreate real-world scenarios. These innovations could transform learning into an engaging experience, leaving workers better prepared for the unexpected.
Proper Usage Techniques for Effective Eye Irrigation
When it comes to proper eye irrigation techniques, the mantra is straightforward: flush thoroughly and don’t stop. A continuous 15-minute rinse is essential for removing harmful substances and minimizing the risk of lasting damage. This isn’t just advice—it’s the gold standard for giving your eyes the best chance at recovery.
However, even the most effective techniques are useless if the eye wash station isn’t within easy reach. Safety protocols emphasize that stations should be accessible within 10-15 seconds of exposure to hazardous materials. Quick access can mean the difference between a minor incident and a severe injury. That’s why strategically placed, user-friendly stations are indispensable—they’re true lifesavers.
Looking ahead, could smarter designs revolutionize these stations? Imagine features like intuitive controls or automated systems that activate instantly. Such advancements could streamline emergency responses, providing workers with the assistance they need precisely when they need it most.
Importance of Regular Training for Construction Workers
For construction workers, consistent eye wash training isn’t just another task—it’s a critical safeguard. This training ensures that every team member knows exactly how to respond in an emergency, significantly reducing the likelihood of severe eye injuries. By teaching workers how to operate eye wash stations and ensuring they know their locations, these programs cultivate a safer workplace where quick, informed actions can make all the difference.
To truly resonate, training sessions should extend beyond the basics. Effective training programs should include:
- Hands-on exercises to practice real-life scenarios.
- Live demonstrations to showcase proper techniques.
- Discussions tailored to the unique risks of each job site.
When workers are thoroughly prepared, the entire team benefits from a stronger safety culture and fewer accidents.
And as the construction industry continues to innovate, why not channel that same energy into training? Tools like augmented reality or immersive simulations could provide workers with a richer understanding of emergency protocols, making them even more equipped to handle unexpected challenges.